Patrząc na porysowaną i pozbawioną połysku powierzchnię lakieru na swoim samochodzie zaczynamy się zastanawiać co by tu zrobić żeby przywrócić ją do idealnego stanu.
Najprostszym i najpewniejszym rozwiązaniem jest zlecenie usługi polerowania firmie zajmującej się profesjonalnie autodetailingem lub doświadczonemu lakiernikowi.
W zasadzie w tym momencie można by skończyć pisanie powyższego tekstu … jednak prawie każdy chce zostać „bohaterem w swoim domu”, więc zanim sami zabierzemy się do polerownia warto wiedzieć na co zwrócić szczególną uwagę.
Zaczniemy od układu i grubości warstw w oryginalnej, fabrycznie nowej powłoce lakierowej, które zostały przedstawione na rys.1.
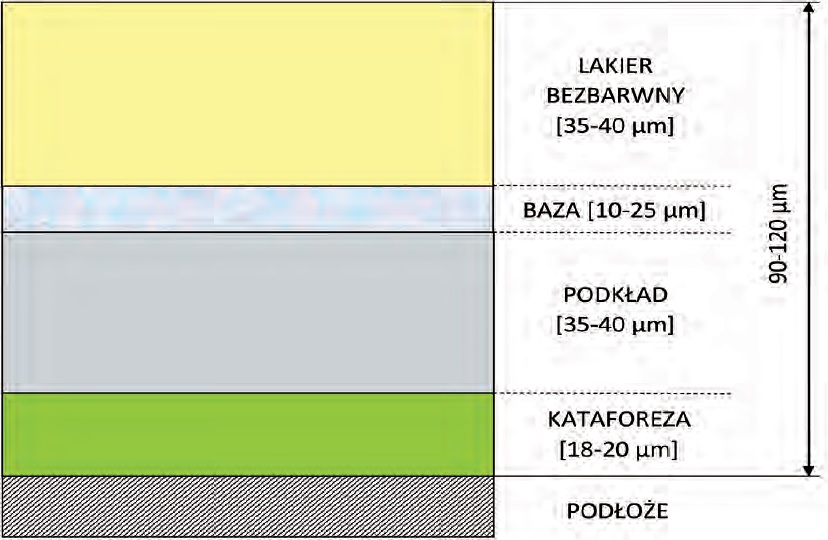
Rys. 1. Układ i średnie grubości warstw w lakierowaniu fabrycznym OEM (system 2-warstwowy – baza + lakier bezbarwny)
Zazwyczaj w lakierowaniu OEM (fabrycznym) w systemie 2-wartwowym uzyskuje się grubości lakieru bezbarwnego w przedziale 35-45µm. Podczas lakierowania renowacyjnego najczęściej uzyskuje się większe grubości. Żeby mieć skalę porównawczą: kartka papieru kserograficznego ma grubość ok. 90-100 µm, zatem warstwa lakieru bezbarwnego z której zamierzamy usunąć rysy to zaledwie połowa tej grubości. W przypadku przecięcia warstwy lakieru bezbarwnego do warstwy bazowej – element będzie musiał zostać ponownie polakierowany. Ta informacja ma uświadomić, że należy zachować szczególną ostrożność podczas polerowania, żeby nie uszkodzić lakieru bezbarwnego.
ZANIM ROZPOCZNIESZ POLEROWANIE:
- Elementy polerowane muszą być dokładnie umyte (najlepiej ręcznie) i wysuszone.
- Sprawdź powierzchnię czy nie ma na niej przyklejonych zanieczyszczeń (naloty przemysłowe, bitumy, smoła, soki z drzew i inne zabrudzenia) – w razie potrzeby użyj zmywacza antysilkonowego. Przy silniejszych zabrudzeniach powierzchni zaleca się użycie glinki polerskiej (mieszanina masy plastycznej i bardzo delikatnego ścierniwa), która skutecznie usuwa większość zanieczyszczeń z powierzchni, aby później nie zabrudzały one materiałów polerskich i gąbki podczas polerowania.
- Zabezpiecz taśmą lakierniczą listwy z tworzywa sztucznego, kierunkowskazy, uszczelki itp. – zapobiegamy zabrudzeniu i wcieraniu się pasty polerskiej w elementy (szczególnie kłopotliwe do usunięcia ze strukturalnego czarnego tworzywa).
OCENA POWIERZCHNI DO POLEROWANIA
- Użyj lampy z silnym światłem do oceny powierzchni (oświetlaj z różnych odległości, również pod kątem żeby najlepiej ocenić stan powierzchni).
- Jeżeli masz możliwość zmierz grubość powłoki lakierowej (przy grubościach całkowitych powłoki poniżej 90µm (co jest bardzo często spotykane przy nowych samochodach) polerowanie zaczyna być bardzo ryzykowne – należy unikać agresywnych past i padów).
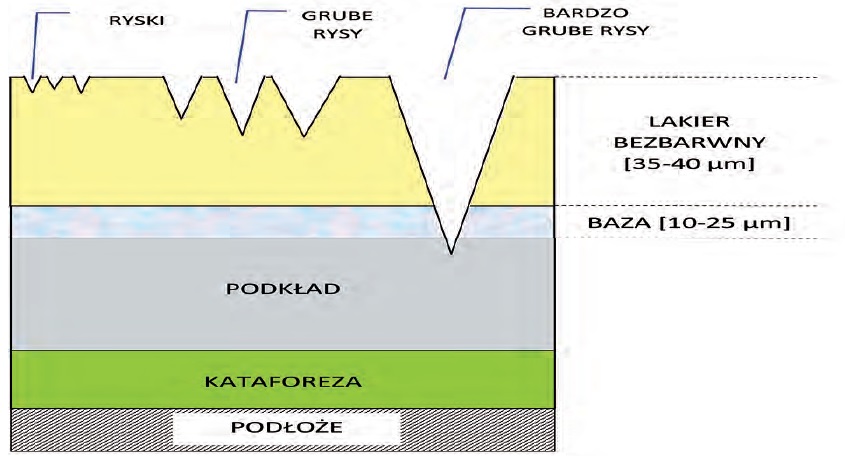
Rys. 2. Wielkości zarysowań w lakierze bezbarwnym w układzie 2-warstwowym (baza + lakier bezbarwny)
POLEROWANIE RÓŻNYCH POWŁOK LAKIEROWYCH:
2-WARSTWOWYCH (BAZA+LAKIER)
Podczas polerowania w systemie 2-warstwowym (baza + lakier bezbarwny) ograniczeniem jest grubość lakieru. W systemach 2-warstwowych przy bardzo grubych rysach przecinających lakier i sięgających do bazy lub podkładu, nie jesteśmy ich w stanie ich usunąć przez polerowanie w taki sposób żeby były one niewidoczne. W praktyce jeżeli przeciągamy po powierzchni lakieru paznokciem
i napotykamy rysę stawiającą opór to rysa jest nie do zapolerowania. W przypadku głębokiej rysy możemy zaokrąglić jej krawędź wówczas będzie się ona mniej „rzucała” w oczy.
1-WARSTWOWYCH (AKRYL)
W przypadku polerowania systemów 1-warstwowych (farby akrylowe) musimy liczyć się z tym, że na skutek zmniejszenia grubości farby akrylowej mogą nastąpić zmiany wybarwienia powłoki. Grubość lakieru akrylowego wynosi ok. 40-50 µm. W systemach 1-warstwowych (najczęściej kolory czerwone) często obserwujemy zjawisko kredowania (odsłonięcie pigmentów na skutek degradacji żywicy) na skutek długotrwałej ekspozycji na promieniowanie słoneczne (UV). Za pomocą polerowania jesteśmy skutecznie przywrócić wyblakły lakier do pierwotnego połysku.
PRZYGOTOWANIE POWIERZCHNI DO POLEROWANIA – szlifowanie
Każdy z producentów materiałów ściernych proponuje swoje własne rozwiązania w zakresie przygotowania powierzchni do polerowania. Warto sięgać po sprawdzone rynkowo rozwiązania, gdyż bardzo często tańsze papiery ścierne robią głębsze rysy niż by to wynikało z opisu gradacji lub bardzo szybko się zużywają.
- Przygotowanie wstępne powierzchni do polerowania będzie zależało od ilości i wielkości wtrąceń lub rys jakie chcemy usunąć w procesie wstępnej obróbki powierzchni. Najczęściej stosowane gradacje papierów przy przygotowaniu wstępnym to:
– przy obróbce ręcznej papiery o gradacjach P1500 i P2000 na mokro,
– przy obróbce mechanicznej papiery o gradacji P1200 i P1500 na sucho (należy pamiętać o stosowaniu miękkiej przekładki).
- Przygotowanie zasadnicze do polerowania umożliwia uzyskanie bardzo gładkiego wykończenia – zmniejsza to nakład pracy znacznie przyspieszając polerowania:
– przygotowanie mechaniczne na mokro (z niewielką ilością wody) przy użyciu specjalistycznych krążków mikrościernych o gradacji P3000, nawet do P6000).
DOBÓR MASZYNY DO POLEROWANIA
Ze względu na rodzaj ruchu polerki dzielimy na:
– rotacyjne (obrotowe)
– rotacyjno-orbitalne.
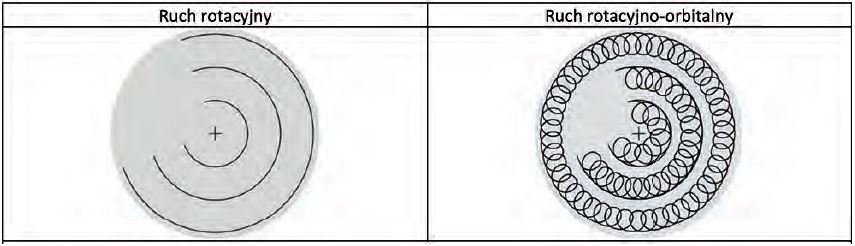
Rys. 3. Podział maszyn polerskich ze względu na wykonywany ruch pada
(źródło: materiały szkoleniowe firmy RUPES)
Na rynku historycznie najbardziej popularne są polerki rotacyjne, lecz coraz większe zainteresowanie wzbudzają polerki rotacyjno-orbitalne. Cechą polerki rotacyjnej jest wysoka obwodowa prędkość liniowa zależna od średnicy pada – łatwo policzyć, że przy średnicy 150 mm i prędkości 2000 obr/min daje to blisko 16 m/s. Tak wysoka prędkość liniowa pozwala na bardzo skuteczną korektę lakieru, lecz z drugiej strony w rękach niewykwalifikowanego operatora niesie duże ryzyko przegrzania i uszkodzenia powłoki lakierowej. Połączenie ruchu rotacyjnego z orbitalnym pozwala zmniejszyć temperaturę powierzchni i ryzyko jej przegrzania. W tabeli poniżej zestawiono najważniejsze cechy polerek rotacyjnych i rotacyjno-orbitalnych.
Mocne strony | Słabe strony | |
Polerka
rotacyjna:
|
Ruch rotacyjny to duża agresywność pozwalająca na wysoki poziom korekcji lakieru |
Wysoka temperatura powierzchni
Hologramy Ryzyko uszkodzenia elementów z tworzyw sztucznych i gumowych Ryzyko uszkodzenia krawędzi Potrzebny wykwalifikowany |
Polerka
rotacyjno-orbitalna:
|
Wypolerowana powierzchnia wolna od hologramów Niewielkie ryzyko Niewielkie ryzyko Krótszy czas polerowania Mniejsza ilość kroków Lepiej sprawdzają się Nie wymagają |
Ruch orbitalny pada utrudnia polerownie w miejscach trudniej dostępnych Słabiej współpracuje z pastami gruboziarnistymi – mniejsza agresywność utrudnia rozpad cząsteczek Słaba współpraca z „tłustymi pastami” – niższa temperatura powierzchni polerowanej powoduje
|
Tab. 1. Zestawienie słabych i mocnych stron polerek rotacyjnych i rotacyjno-oscylacyjnych
(źródło: na podstawie materiałów szkoleniowych firmy RUPES)
![]() |
![]() |
Rys. 4. Elektryczna polerka rotacyjna LH 19E [źródło: RUPES] |
Rys. 4. Elektryczna polerka rotacyjno-orbitalna LHR 21ES [źródło: RUPES] |
NA CO ZWRÓCIĆ UWAGĘ PRZY WYBORZE MASZYNY POLERSKIEJ?
– ergonomiczność konstrukcji polerki (zależna od osobistych preferencji – sposób i komfort uchwytu, umiejscowienie przełączników regulacji obrotów),
– możliwość regulacji obrotów w zakresie 600 do 2000 obr/min.,
– elektroniczna kontrola prędkości – stała prędkość obrotowa niezależnie od nacisku operatora,
– dobre wyważenie maszyny polerskiej pozwalające na łatwe prowadzenie i brak wibracji.
DOBÓR PADA POLERSKIEGO
- A) MATERIAŁ PADA
- WEŁNA (FUTRA POLERSKIE)
Wysokiej jakości futra polerskie są wykonane z naturalnej owczej wełny (np. merynosów) przez co cechują się dużą trwałością. Posiadają dużą zdolność korekcji lakieru, świetnie sprawdzają się na mocno zniszczonych oraz twardych lakierach. Typowe zastosowanie to usuwania drobnych niedoskonałości powstałych na lakierze np. kolistych rysek powstałych po myciu, odświeżanie powierzchni z wyblakłym lakierem, itp.
- GĄBKI
Gąbki polerskie wykonane są z pianki poliuretanowej o strukturze komórkowej. Istotne jest aby struktura komórek była otwarta, gdyż zapewnia to przepływ powietrza wspomagając chłodzenie powierzchni. Otwarta struktura komórkowa to również mniejsza tendencja do zapychania i możliwość stopniowego oddawania pasty podczas polerowania zapewniająca lepsze właściwości korekcyjne.
Twardość gąbki:
Producenci gąbek polerskich zazwyczaj dostarczają pady o różnych twardościach dających różne możliwości korekcyjne. Najczęściej stosowane są systemy kolorów do oznaczanie poszczególnych twardości gąbek.
Stopień twardości | Charakterystyka i przeznaczenie |
TWARDE![]() |
– najlepsze właściwości ścierne
– zalecane do operacji wstępnych z użyciem gruboziarnistych past polerskich – doskonałe na stare lakiery |
ŚREDNIE![]() |
– właściwości polerujące
– zalecane do użycia z średnioziarnistymi pastami polerskimi – uniwersalne w zastosowaniu (stare i nowe lakiery) |
MIĘKKIE![]() |
– najlepsze na prace wykończeniowe
– zalecane do operacji wykańczających z użyciem drobnoziarnistych past polerskich lub mleczek polerskich – minimalizują ryzyko przegrzania powierzchni i powstawania hologramów – zalecane w szczególności do ciemnych kolorów |
Tab. 2. Charakterystyka i przeznaczenie gąbek w zależności od ich stopnia twardości [źródło: NOVOL]
Struktura powierzchni kontaktowej gąbki z powierzchnią polerowaną:
Karbowana – stosowana do prac wykończeniowych przy użyciu mleczek polerskich. Kontakt z powierzchnia mają tylko wypukłości (karby) przez co powierzchnia styku jest mniejsza co pozwala na pracę przy większych obrotach i nie powoduje efektu przypalania pasty polerskiej.
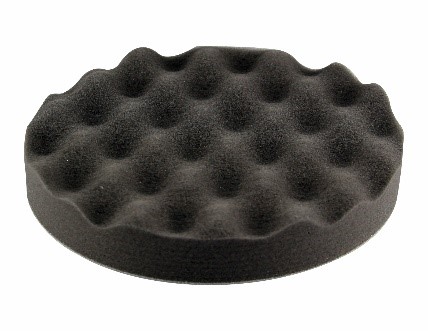
Rys. 4. Karbowana gąbka do prac wykończeniowych z systemu polerskiego QUATTRO [źródło: NOVOL]
Frezowana (nacięcia) – funkcją nacięć jest zatrzymywanie pasty polerskiej na powierzchni gąbki i późniejsze równomierne oddawanie jej na polerowany element. Chronią również przed nadmiernym rozpryskiwaniem przez utrzymywanie nadmiaru pasty w nacięciach.
- UKŁADY HYBRYDOWE (GĄBKA + WEŁNA)
W układzie hybrydowym futro jest osadzone na gąbce polerskiej. Takie układy cechują się umiarkowany stopniem ścieralności połączonym z dobrą redukcją ciepła, dzięki czemu zabezpieczają lakier przed uszkodzeniem.
- B) ŚREDNICA PADA
Średnica pada ma bezpośredni wpływ na jego agresywność. Związane jest to prędkością liniową na obwodzie, która jest wynikiem prędkości obrotowej polerki i średnicy pada. Im wyższa prędkość liniowa tym skuteczniejsza korekta, ale również wyższe wspomniane już ryzyka związane z przegrzaniem powierzchni i przypaleniem powłoki lakierowej.
Średnica [”] | Średnica [mm] | Prędkość obrotowa [obr/min] | Prędkość obwodowa [m/s] |
4 | 101,6 | 600 | 3,2 |
1000 | 5,3 | ||
1500 | 8 | ||
6 | 152,4 | 600 | 4,8 |
1000 | 8 | ||
1500 | 12 | ||
8 | 203,2 | 600 | 6,4 |
1000 | 10,6 | ||
1500 | 16 |
Tab. 3. Prędkość obwodowa w zależności od średnicy pada i zadanej prędkości obrotowej polerki
- C) SPOSÓB MOCOWANIA PADA
– mocowanie bezpośrednie – gąbka polerska jest na stałe połączona z talerzem oporowym, zaletą jest powtarzalne centryczne mocowanie na maszynie polerskiej,
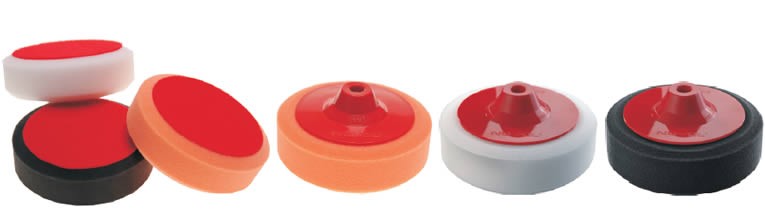
Rys. 5. Gąbki polerski mocowane bezpośrednio na maszynie polerskiej [źródło: NOVOL]
– mocowanie pośrednie – za pomocą talerza oporowego (talerz oporowy jest zamocowany do polerki na standardowy gwint M14, na talerzu znajduje się rzep przez co możliwa jest szybka zmiana gąbek podczas polerowania).
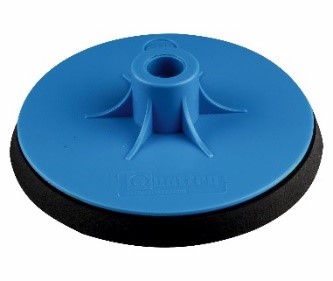
Rys. 6. Talerz oporowy na rzep z systemu polerskiego QUATTRO [źródło: NOVOL]
KULKI POLERSKIE
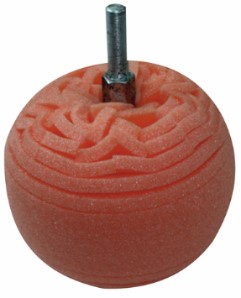
Rys. 7. Kulka polerska z systemu polerskiego QUATTRO [źródło: NOVOL]
W przypadku trudnodostępnych miejsc (np. wnękach i wgłębieniach) doskonałym rozwiązaniem są kulki polerskie wykonane z gąbki poliuretanowej. Struktura gąbki umożliwia zatrzymanie wody w jej wnętrzu, co przyspiesza odprowadzenie ciepła z polerowanej powierzchni. Kulka jest zakończona trzpieniem umożliwiającym współpracę z wiertarką. Świetnie sprawdzają się np. przy polerowaniu felg.
DOBÓR PASTY POLERSKIEJ
Mnogość producentów oferujących pasty polerskie może przyprawić o zawrót głowy. Każdy z producentów proponuje swój własny system o różnej złożoności dla osiągniecia jak najlepszego efektu.
W niniejszym artykule chciałem krótko przedstawić system polerski QUATTRO opracowany przez firmę NOVOL.
System polerski QUATTRO to system 2 etapowy:
ETAP 1
Pasta polerska QUATTRO
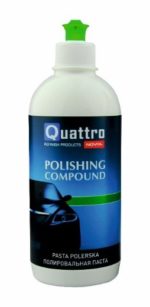
Rys. 8. Polishing Compound – pasta polerska QUATTRO [źródło: NOVOL]

Rys. 9. Rozpad cząsteczek ścierniwa pasty podczas polerowania
ETAP 2
Mleczko polerskie QUATTRO
Rys. 10. Finishing Glaze – mleczko polerskie QUATTRO
Mleczko polerskie QUATTRO jest mieszaniną bardzo drobnego materiału ściernego i specjalnego nośnika. Bardzo drobny materiał ścierny konieczny jest do dopracowania powierzchni w szczególności na lakierach świeżych, gdzie podłoże nie jest wystarczająco utwardzone, żeby mógł nastąpić całkowity rozpad cząsteczek pasty polerskiej. Nieroztarte cząsteczki pasty powodują powstawanie mikrodefektów na powierzchni. Mleczko polerskie QUATTRO możemy wykorzystać do odświeżania niezbyt zniszczonych powłok, uzyskania bardzo wysokiego połysku na starych lakierach lub jako wykończenie przy usuwaniu hologramów na lakierach świeżych.
System QUATTRO jest maksymalnie prosty w użytkowaniu i jednocześnie daje bardzo szybki efekt trwałej korekty powłoki lakierowej. Pasta bardzo dobrze rozprowadza się na gąbce i na elemencie. Co ważne przy zabrudzeniu pastą sąsiadujących elementów (szczególnie z tworzywa sztucznego) możemy ją zmyć wodą bez większego problemu.
![]() |
![]() |
![]() |
|
Rys. 11. Technologia QUATTRO – przygotowanie powierzchni i dobór twardości gąbki polerskiej dla pasty i mleczka polerskiego |
Przebieg procesu polerowania w systemie QUATTRO
- W celu usunięcia wtrąceń, zanieczyszczeń lub nadmiernej struktury (np. „skórka pomarańczy”) powierzchnię przeznaczoną do polerowania należy wstępnie przeszlifować papierem ściernym o gradacji P2000-P2500.
- Przy polerowaniu na sucho nanieść niewielką ilość pasty na suchą gąbkę i na element, przy polerowaniu na mokro pastę należy nanosić w ten sam sposób, ale na wilgotną gąbkę (zamoczoną w wodzie i odwirowaną).
- Do polerowania używamy polerki maszynowej (elektrycznej lub pneumatycznej) w zakresie obrotów 1000-2000 obr/min z gąbką polerską białą (twardą) lub pomarańczową (średniej twardości).
- Polerujemy z lekkim lub średnim naciskiem na polerkę, odpowiednio dopasowując obroty tak, aby nie przegrzać lakieru, a jednocześnie uzyskać wymagany efekt. Powtarzamy czynność, aż do zupełnej likwidacji rys.
- Podczas polerowania w momencie, gdy pasta polerska zaczyna podsychać, zbieramy zaschnięty nadmiar pasty za pomocą wilgotnej ściereczki lub zraszamy delikatnie powierzchnię elementu wodą, redukujemy nacisk polerki i kontynuujemy polerowanie.
- Po zakończonej pracy nadmiar produktu lub zabrudzenia na powierzchni z tworzyw sztucznych i sąsiadujących elementów usuwamy przy pomocy zwilżonej ściereczki.
- Zakończoną pracę polerską należy ocenić wizualnie porównując np. połysk i strukturę lakieru z sąsiadującymi elementami.
Ważne parametry przy wyborze systemów polerskich:
– czas polerowania (możliwość uzyskania szybkiej korekcji delikatnych rys po szlifowaniu drobnoziarnistymi papierami ściernymi),
– możliwość uzyskania wysokiego i trwałego połysku (brak w składzie silikonów i wosków, nadających „sztucznego połysku” znikającego po czasie),
– możliwość pracy na mokro i ma sucho,
– stosowanie do lakierów świeżych i w pełni utwardzonych,
– łatwość do usunięcia zabrudzeń z tworzywa sztucznego.
Ważne parametry przy wyborze systemów polerskich:
– czas polerowania (możliwość uzyskania szybkiej korekcji delikatnych rys po szlifowaniu drobnoziarnistymi papierami ściernymi),
– możliwość uzyskania wysokiego i trwałego połysku (brak w składzie silikonów i wosków, nadających „sztucznego połysku” znikającego po czasie),
– możliwość pracy na mokro i ma sucho,
– stosowanie do lakierów świeżych i w pełni utwardzonych,
– łatwość do usunięcia zabrudzeń z tworzywa sztucznego.
PODSUMOWANIE
Polerowanie powłoki lakierowej nie jest bynajmniej prostym zadaniem. W zasadzie powinniśmy mówić o technologii polerowania. Każdy element składowy tej technologii począwszy od przygotowania powierzchni do polerowania, doboru pada (rodzaju, twardości i wielkości), doboru sytemu pasty polerskiej, techniki polerowania (ilości przejść, prędkość obrotowa, nacisku na powierzchnię) ma ogromny wpływ na efekt końcowy. Ważne jest także przestrzeganie zaleceń technologicznych producenta i zachowanie ostrożności, żeby zamiast uzyskania olśniewającego połysku nie być zmuszonym do wizyty u lakiernika, aby polakierować element z przetartym lakierem.
Dodaj komentarz
Musisz się zalogować, aby móc dodać komentarz.